Customer Stories / Retail and Wholesale
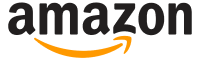
Amazon Customer Fulfillment Increased Productivity and Reduced Unplanned Equipment Downtime Using Amazon Monitron
Learn how Amazon Customer Fulfillment in the retail and wholesale industry reduced unplanned equipment downtime by 69 percent using Amazon Monitron.
69%
reduction in unplanned equipment downtime hours
$22.75 million
saved by avoiding unplanned downtime, lost production hours, and late shipment costs
Increased
staff productivity
Achieved
return on investment in under 1 year
Overview
At Amazon, customer obsession is a company-wide principle, and the company expects its fulfillment centers to meet customer promises for timely order delivery. Packages at fulfillment centers daily traverse miles of conveyor and sorter systems, so Amazon Customer Fulfillment needs its equipment to operate reliably.
To achieve high reliability of its industrial equipment, Amazon Customer Fulfillment turned to Amazon Web Services (AWS) and started implementing Amazon Monitron, an end-to-end condition-monitoring system that uses machine learning to detect potential failures in industrial equipment. Using Amazon Monitron, Amazon Customer Fulfillment implemented predictive maintenance to reduce unplanned equipment downtime by 69 percent, which helps the company deliver customer orders on time.
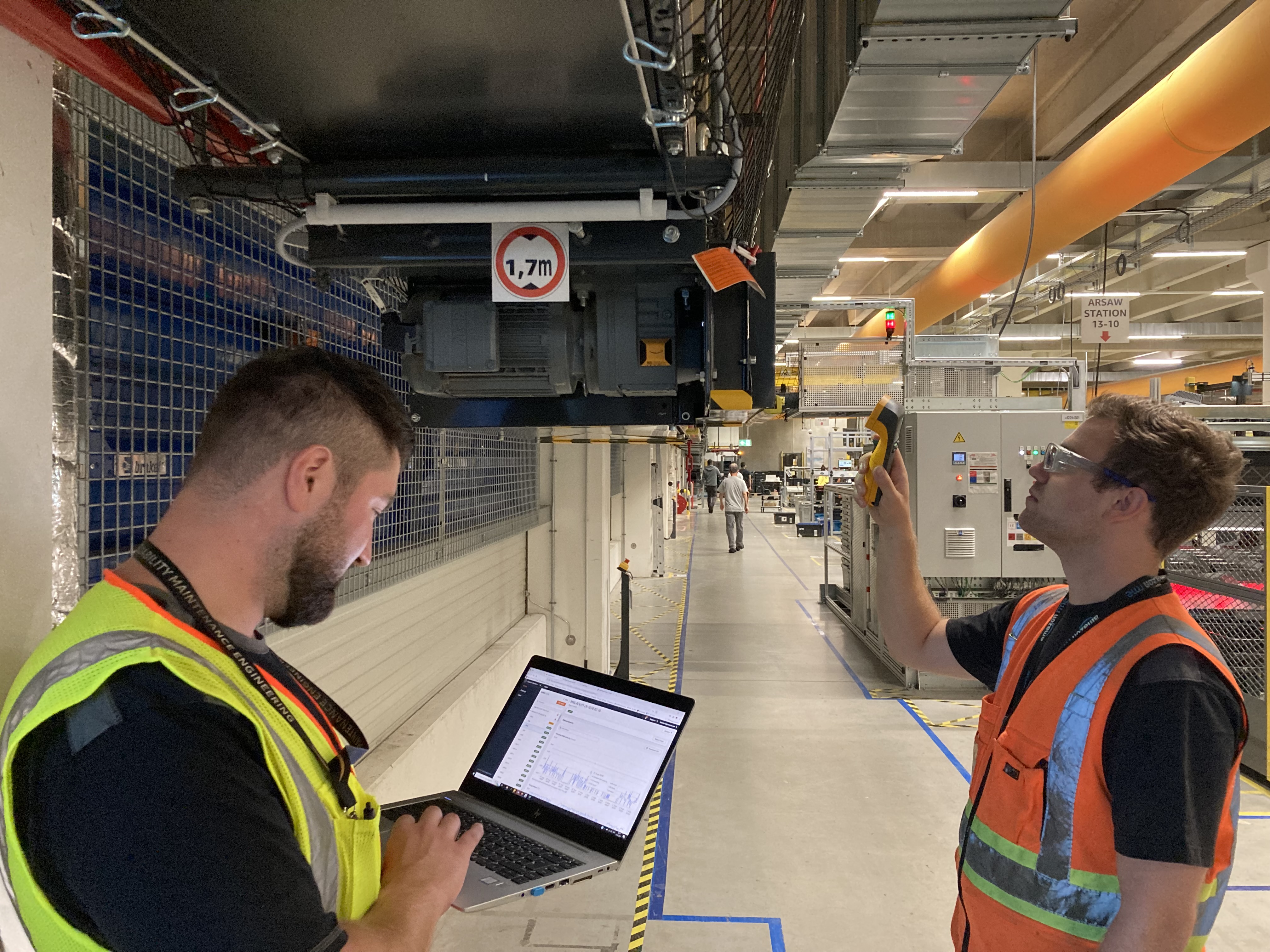
Opportunity | Preventing Costly Unplanned Equipment Downtime Using Amazon Monitron
Amazon, one of the largest online retailers and a prominent cloud service provider, has hundreds of fulfillment centers worldwide. When a customer makes an online purchase, employees at Amazon Customer Fulfillment pick, pack, and ship the order.
At each fulfillment center, up to 80 engineers are responsible for maintaining the equipment. Because of the amount of rotating equipment to maintain, fulfillment centers couldn’t cost-effectively scale previous condition-monitoring programs, such as ultrasound, thermography, and oil analysis. Prior to implementing Amazon Monitron, technicians walked around the site to take readings, manually analyzing the measurements to determine the condition of the equipment. Amazon Customer Fulfillment sometimes experienced unplanned equipment downtime when a problem occurred before a technician could take a reading and identify the issue. Unplanned downtime can be costly and delay customer deliveries. For example, if a critical sorter fails for 3 hours during the peak Christmas period, it can lead to the late delivery of over 30,000 orders.
Amazon Customer Fulfillment wanted to implement a predictive maintenance program as part of its broad maintenance strategy to improve equipment reliability and reduce overall maintenance costs. However, predictive maintenance solutions can be time consuming and expensive to purchase, install, and commission, often requiring subject matter experts to analyze data to detect potential failures. Having thousands of pieces of industrial equipment in each fulfillment center, Amazon Customer Fulfillment looked to Amazon Monitron as a cost-effective condition-monitoring solution, which uses wireless sensors to capture vibration and temperature data and automatically creates a machine learning model to detect potential failures in rotating equipment like motors, gearboxes, and bearings. Because Amazon Monitron doesn’t require condition-monitoring expertise to install or use, the company’s maintenance technicians could install the wireless sensors and set them up in the Amazon Monitron app quickly. “Implementing Amazon Monitron couldn’t get any simpler unless the sensors could glue themselves on,” says Luke Grice-Lowe, reliability engineer at Amazon Customer Fulfillment. The company tested Amazon Monitron at scale in one of its sites in Europe between August 2020 and May 2021, detecting 68 potential failures in 10 months by monitoring 792 assets. The company expanded to another 25 sites by the end of 2021 because of the positive results.

Using Amazon Monitron, technicians go from being reactive to proactive. You’re no longer waiting for something to break down. You’re already there planning and working on it.”
Luke Grice-Lowe
Reliability Engineer, Amazon Customer Fulfillment
Solution | Increasing Reliability While Decreasing Costs Using Amazon Monitron
Amazon Customer Fulfillment reduced its unplanned equipment downtime hours on equipment monitored by Amazon Monitron by 69 percent, according to a comparison of data from 9 months before the implementation with the same period after going live. “A key consideration is that there could be 13 packers working on one process path,” says Grice-Lowe. “Every hour that process path is down would represent 13 hours of lost time packing for customers.” By reducing unplanned downtime and the downstream effects, the company significantly decreases the likelihood of late deliveries. Also, because Amazon Monitron detects potential failures early, maintenance engineers can scope, plan, and execute a repair outside of operational hours.
Using Amazon Monitron, the company receives automatic temperature and vibration measurements every hour, detecting potential failures within hours compared with 4 weeks for the previous handheld techniques. Using Amazon Monitron and Amazon Kinesis Data Streams, a serverless service for streaming data at virtually any scale, Amazon Customer Fulfillment creates maintenance work orders when a potential failure is detected. Because measurement details and insights are included in the work order, technicians can limit time spent on record keeping and focus on value-added tasks that improve reliability and extend equipment life. Technicians can also detect common failure modes and improve the overall maintenance strategy with better work order data quality. “One of the biggest draws of Amazon Monitron is that we can set it up and forget about it until we need to pay attention,” says Grice-Lowe. “With the amount of work and labor requirements for the sites, it’s one less thing the technicians need to worry about.”
Amazon Customer Fulfillment anticipated that the cost savings realized by implementing Amazon Monitron would pay for the solution in about 2 years. After starting the implementation, the company analyzed 25 live sites and calculated that it had saved enough money to achieve a return on investment in under 1 year, significantly earlier than expected. As of 2022, Amazon Customer Fulfillment had saved an estimated $2.75 million in lost production hours, the amount of time that unplanned equipment downtime prevents associates from working. Amazon Customer Fulfillment saved an additional $20 million in downstream logistical and productivity costs that it would have incurred to make sure it delivered customer orders even when unplanned downtime had occurred. As the company expands to use Amazon Monitron at more sites, it anticipates realizing additional cost savings. “Using Amazon Monitron, we can switch from calendar-based maintenance, where we look at the same asset regardless of the need every month, to a more targeted approach of letting the machine tell us when it needs work or intervention, which is key for addressing increasing costs around the world,” says Grice-Lowe.
Outcome | Expanding to Cover New Sites Globally
Because of the performance, ease of use, and affordability that Amazon Monitron delivers, Amazon Customer Fulfillment is scaling to deploy it at existing and new fulfillment centers across the North America, Europe, and Asia Pacific regions. Amazon Customer Fulfillment also plans to invest further in the solution at existing sites by fine-tuning the thresholds that invoke alarms and expanding into other areas like monitoring control equipment. “Using Amazon Monitron, technicians go from being reactive to proactive,” says Grice-Lowe. “You’re no longer waiting for something to break down. You’re already there planning and working on it.”
About Amazon Customer Fulfillment
Amazon, one of the largest online retailers and a prominent cloud service provider, has hundreds of fulfillment centers around the globe. When a customer makes a purchase, employees at the fulfillment centers pick, pack, and ship the order.
AWS Services Used
Amazon Monitron
Amazon Monitron is an end-to-end condition monitoring system that uses machine learning to automatically detect abnormal conditions in industrial equipment and lets users implement predictive maintenance to reduce unplanned downtime.
Amazon Kinesis Data Streams
Amazon Kinesis Data Streams is a serverless streaming data service that makes it easy to capture, process, and store data streams at any scale.
Learn more »
Explore Amazon's journey of innovation using AWS
More Amazon Stories
Get Started
Organizations of all sizes across all industries are transforming their businesses and delivering on their missions every day using AWS. Contact our experts and start your own AWS journey today.